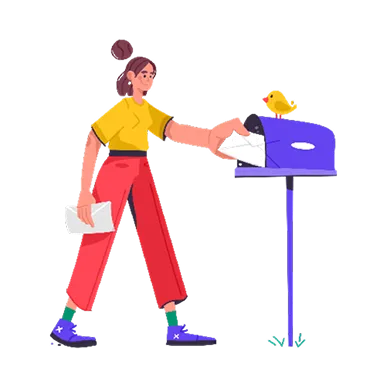
What is Takeoff in Construction?
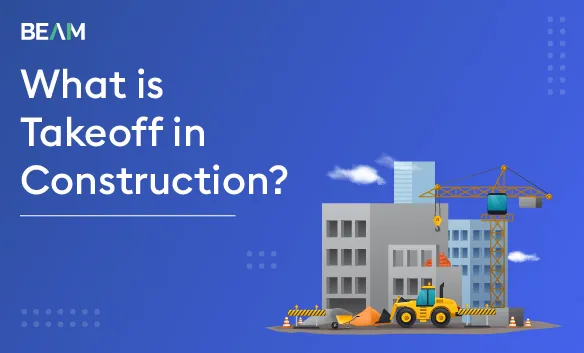
Behind every impressive construction project, from towering skyscrapers to state-of-the-art facilities, lies a critical process that serves as the foundation for success: the construction takeoff.
While it may seem like a relatively straightforward task, the takeoff is a meticulous and detailed process that involves carefully analyzing architectural drawings, blueprints, and specifications to determine the quantities of materials required for a project. Without accurate takeoffs, even the most well-planned construction ventures can quickly derail, resulting in costly overruns, material shortages, or scheduling delays.
In this era of technological advancement, the art and science of takeoff has evolved, embracing innovative tools and software solutions that streamline the process and minimize the risk of human error. Yet, at its core, the takeoff remains a testament to the skill and expertise of those who do it. In this blog, we will explore the nuances of construction takeoff, challenges, and best practices that separate a good takeoff from a bad one.
What is the meaning of Takeoff in Construction?
In the construction industry, the term "takeoff" refers to the process of carefully reviewing and quantifying the materials required for a particular project. Essentially, It involves meticulously analyzing architectural drawings, blueprints, and specifications to determine the quantities of various components needed to complete the work.
For instance, an electrical takeoff might include the linear footage of conduit, categorized by size. It would also include a count of outlets, switches, and light fixtures. Similarly, a plumbing takeoff would specify the length of pipes by size and material along with the number and type of fittings and fixtures.
What is the Purpose of Takeoff in Construction?
The purpose of a takeoff is to provide a comprehensive and accurate list of required materials, which is essential for generating cost estimates and project schedules. Without a precise takeoff, estimates can be severely flawed, leading to costly overruns or underestimations that can jeopardize the project's success.
Accurate takeoffs contribute significantly to project success by:
- Enabling realistic cost estimation: A detailed takeoff enables estimators to accurately calculate material, labor, and equipment costs, ensuring that project bids are competitive yet profitable.
- Facilitating resource planning: By quantifying the required resources, takeoffs help construction teams plan for material procurement, labor allocation, and equipment rentals or purchases.
- Minimizing waste and overruns: Precise takeoffs minimize excess material waste and reduce the likelihood of costly overruns due to underestimated quantities.
Difference between Quantity Takeoff and Material Takeoff
While both quantity takeoff (QTO) and material takeoff (MTO) involve quantifying resources, they have subtle differences:
- Quantity Takeoff (QTO): This is a broader process encompassing all the resources required to complete a construction project. It includes not only materials but also labor hours, equipment needs, subcontractor scopes of work, permits, and fees. The primary purpose of a QTO is to generate a cost estimate for the entire project.
- Material Takeoff (MTO): This focuses solely on identifying and quantifying the materials needed to complete a specific construction element or the entire project. This includes lumber, concrete, bricks, drywall, electrical wiring, plumbing supplies, and more. The primary purpose of an MTO is to determine the exact amount of materials required for procurement.
In simpler terms, a Quantity takeoff provides a bigger picture of project resources, while the Material takeoffs provides in into the specific materials required. While they serve different purposes, they are often used together in the construction process. A QTO might inform the overall project cost, and an MTO derived from it would detail the materials needed to stay within that budget.
How to Perform a Takeoff?
Construction takeoff serves as the foundation for accurate cost estimation and project planning. But how exactly do you translate blueprints into a precise list of materials? Here's a breakdown of the steps involved in performing a takeoff:
Step 1: Review Project Drawings and Specifications
The first step in performing a construction takeoff is to thoroughly review the project drawings and specifications provided by the architect or engineer. These documents outline the scope of work, trades involved, dimensions, and materials required for each component of the project.
Step 2: Identify Measurement Types
Break down the project into smaller, more manageable sections. This could involve focusing on floors, walls, roofs, or specific building systems like plumbing or electrical. Next, it's crucial to identify the types of measurements required for the materials involved in the project. The four primary measurement types include count, length, area, and volume. Each measurement type corresponds to specific materials and construction elements within the project.
Step 3: Perform Takeoff Calculation
Once the measurement types are identified, contractors can begin the takeoff calculation process. This involves systematically quantifying the materials needed based on the dimensions provided in the project drawings. For simpler projects, contractors can manually measure dimensions from printed drawings and calculate quantities for each material.
For complex projects or increased efficiency, contractors can utilize software like Beam AI. This software streamlines the process by allowing them to input dimensions directly from digital drawings and automatically calculate material quantities
How to Takeoff Different Kinds of Materials?
When taking quantities for a project, contractors need to account for various types of materials, each with its own unique calculation method. While some materials may require simple counts or linear measurements, others necessitate more complex area or volume calculations. Here's how different materials are typically calculated during a takeoff:
Raw materials: For raw materials like lumber, steel, or piping, contractors need to carefully measure and record dimensions such as length, width, depth, and weight. These measurements are then used to calculate the precise quantities required for the project.
Manufactured fixtures: In the case of manufactured fixtures like windows, doors, or light fixtures, contractors typically only need to provide the estimated quantity needed, as these items often come with set prices from suppliers, so the focus is on determining the counts of items needed rather than detailed measurements.
Materials for flat surfaces: When dealing with materials used for flat surfaces, such as drywall panels, flooring tiles, or roofing materials, contractors need to calculate the total area to be covered. This information is then used to determine the required quantities, taking into account factors like waste and overlap.
Bulk materials: For bulk materials like concrete, gravel, or insulation, contractors must calculate the volume required. This is typically done by analyzing the blueprint dimensions and calculating the cubic yardage necessary to fill designated spaces.
In addition to material calculations, takeoffs also involve quantifying other project components, such as labor hours, equipment needs, and any necessary subcontractor services. By accurately accounting for all aspects of the project during the takeoff process, contractors can generate reliable cost estimates, facilitate resource planning, and minimize the risk of material waste or costly overruns.
Common Challenges in Construction Takeoffs
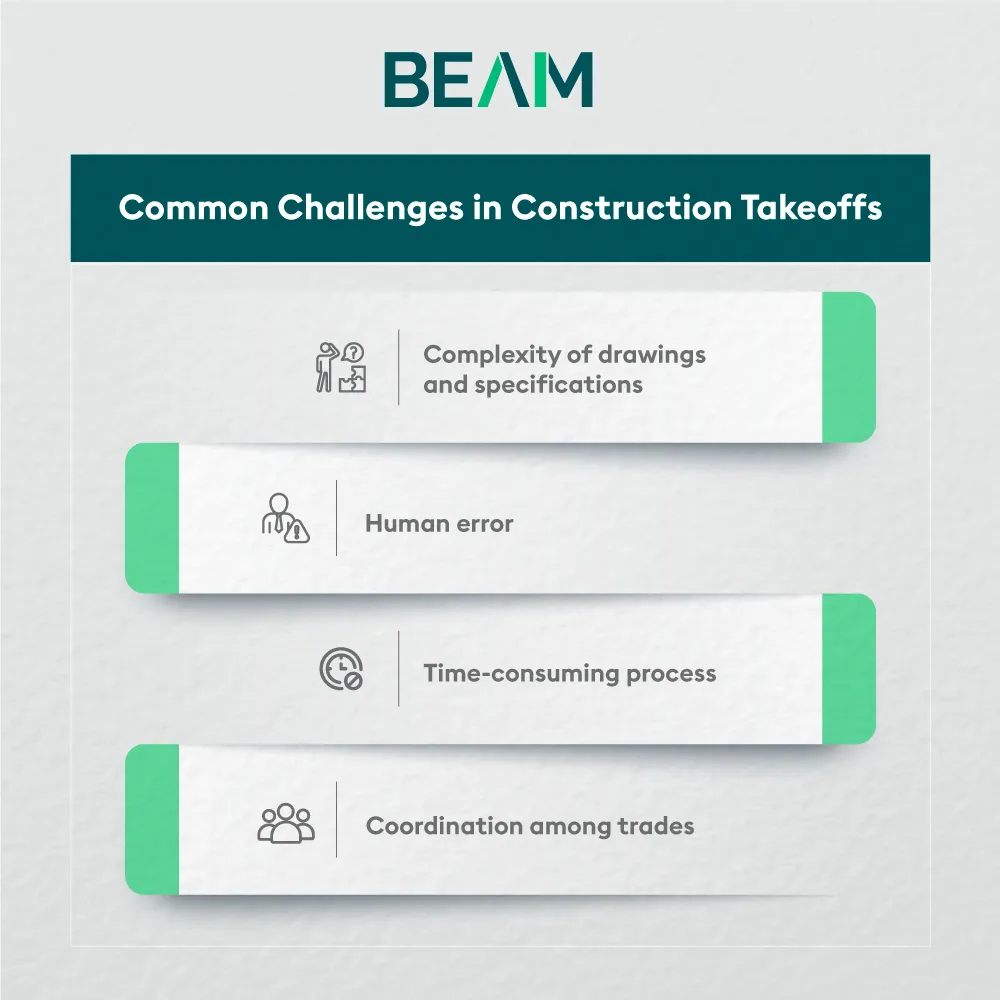
While takeoffs are critical to project success, the process is not without its challenges. Construction professionals must be vigilant and employ best practices to overcome potential obstacles that can lead to inaccurate quantity estimates and/or project delays. Some of the common challenges include:
1. Complexity of drawings and specifications
Construction documents, including architectural drawings, structural plans, and technical specifications, can be highly complex and require a deep understanding of construction terminology, symbols, and standards. Interpreting these documents accurately is crucial for a precise takeoff.
2. Human error
Manual takeoffs done by examining plan specs involve numerous calculations, measurements, and cross-referencing of information. Even experienced professionals can make mistakes, such as miscalculations, overlooking details, or misinterpreting specifications, leading to inaccurate estimates.
3. Time-consuming process
Performing a comprehensive takeoff can be extremely time-consuming, especially for large-scale or intricate projects. The effort required to analyze every detail and quantify all components can be substantial.
4. Coordination among trades
Construction projects often involve multiple trades and subcontractors, each with their own specific materials and equipment requirements. Ensuring accurate coordination and communication among these trades during the takeoff process is essential to avoid conflicts, overlaps, or omissions in the overall material and resource quantification.
Best Practices for Construction Takeoffs:
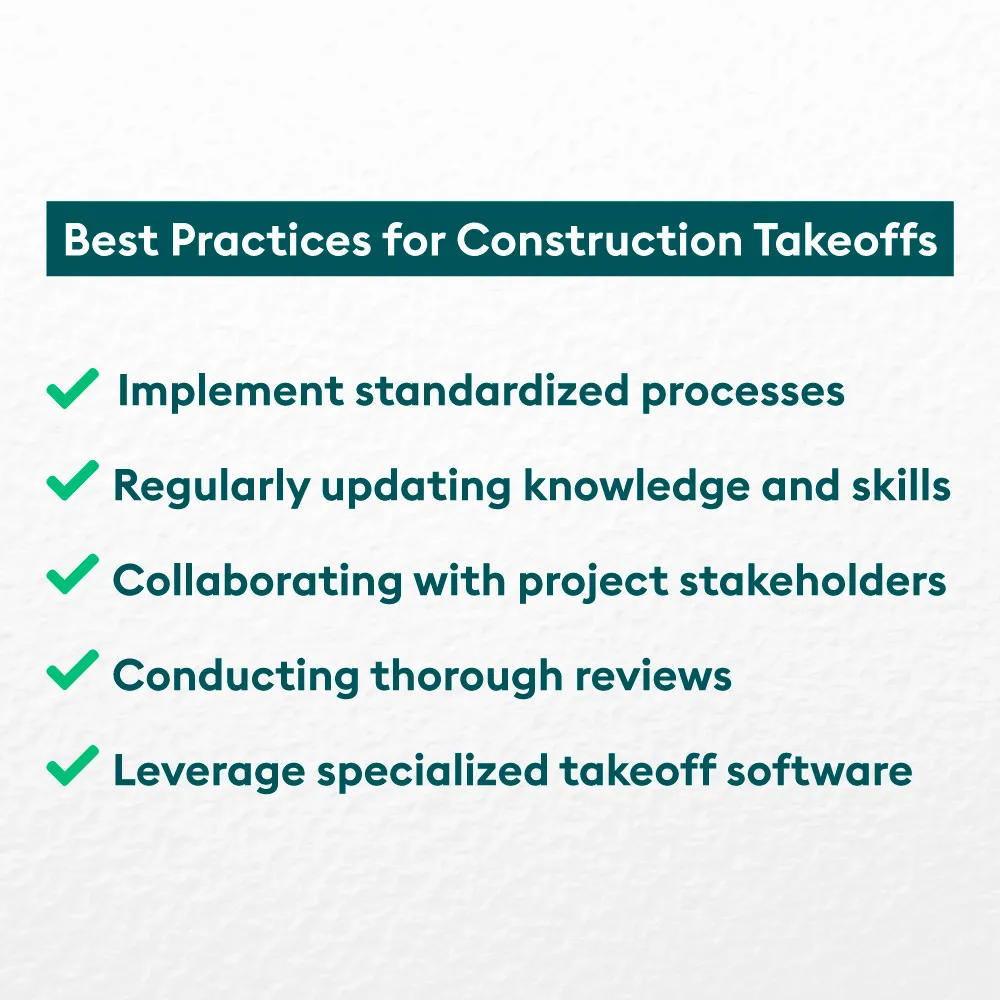
To overcome the challenges associated with construction takeoffs and ensure accuracy, contractors and estimators should adopt a set of best practices that leverage technology, standardized processes, and collaboration.
1. Implement standardized processes
Establishing clear and consistent procedures for performing takeoffs, such as standardized checklists, templates, and workflows, can help minimize mistakes and ensure consistency across projects and team members.
2. Regularly updating knowledge and skills
The construction industry is constantly evolving, with new materials, techniques, and technologies emerging regularly. Estimators and takeoff professionals must stay up-to-date with these changes through continuous training and education to ensure accurate and current takeoffs.
3. Collaborating with project stakeholders
Effective communication and collaboration among all project stakeholders, including architects, engineers, contractors, and subcontractors, can help identify potential issues, discrepancies, or ambiguities early in the takeoff process, allowing for timely resolution and ensuring a more accurate final product.
4. Conducting thorough reviews
Implementing a rigorous review process, involving multiple team members with different perspectives and expertise can help catch errors, oversights, or inconsistencies before they impact the project. Regular peer reviews and cross-checking of takeoff quantities can significantly improve accuracy.
5. Leverage specialized takeoff software
Advanced software like Beam AI is designed specifically to streamline the process, reduce errors, and improve accuracy. The takeoff software utilizes artificial intelligence to automatically and accurately provide a number of materials for every type of trades in construction.
The Bottom Line: Emerging Trends in Takeoff Technology
Construction takeoff is not just a preliminary step in project planning; it's a critical process that sets the stage for project success. As the construction industry continues to evolve, so do the tools and technologies used for takeoffs. One exciting development is the potential for artificial intelligence (AI) and machine learning to automate aspects of the takeoff process.
AI-powered takeoffs like Beam AI can analyze digital construction documents, including drawings and specifications, and automatically identify and quantify different material components with 99%+ accuracy with faster turnaround. This helps in reducing the time spent on the takeoff process and shifts focus toward other impactful tasks.
As takeoff technology continues to advance, construction professionals should stay informed about the latest developments and consider adopting tools that can improve efficiency, accuracy, and ultimately, project success.