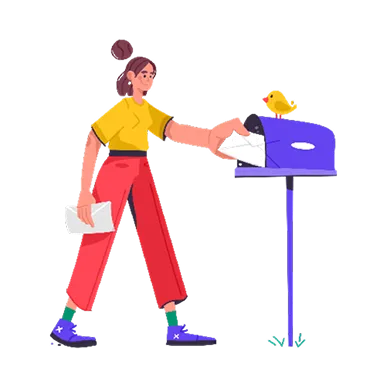
Demolition Takeoffs 101: All You Need to Know to Get it Right!
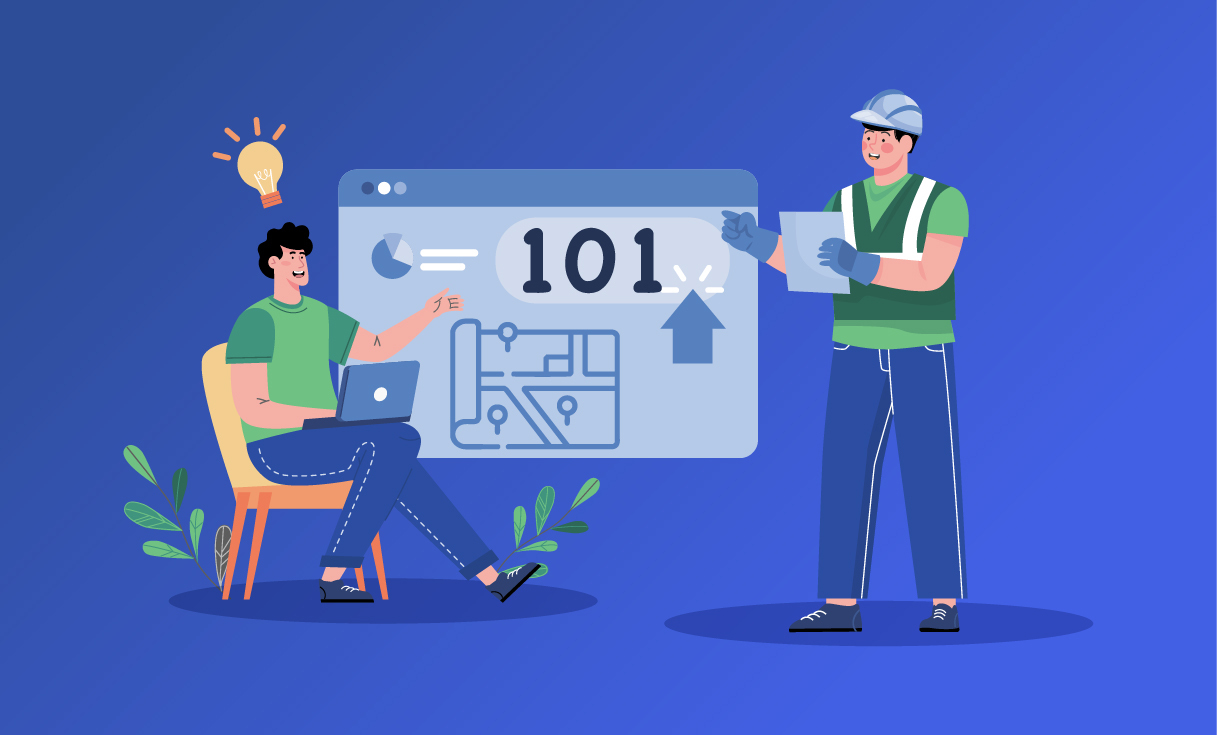
Before the first brick is laid or beam installed, one critical step can make or break your project timeline and budget: demolition takeoffs.
Many still see demolition as straightforward, but there is a lot of strategy behind getting it just right. Demolition takeoff is the process of identifying and quantifying all materials, labor, and equipment required to partially or fully remove an existing structure. The accuracy of these demolition estimates forms the foundation of effective preconstruction and site preparation for any construction project.
In short, think of it as your ‘unbuilding plan”.
This guide includes everything you need to know about demolition takeoffs and the importance of accurate demolition estimates. You'll learn the fundamentals, follow a step-by-step demolition takeoff process, and discover how technology transforms traditional demolition methods.
Whether you're an estimator, contractor, or curious project manager, you're at the right place. Let's begin!
Demolition Takeoff Fundamentals: Methods, Types & Basic Takeoff Components
An accurate demolition estimate starts with understanding the core elements of a demolition takeoff. Whether removing a single wall or tearing down an entire structure, the takeoff accuracy depends entirely on how well you define your scope, materials involved, and the required demolition method.
What Does a Demolition Estimator Do?
A demolition estimator is responsible for:
- Conducting site walks and reading blueprints.
- Creating detailed demolition cost calculations.
- Coordinating with safety leads and site supervisors.
- Leveraging demolition takeoff software to speed up and refine bid preparation.
What’s Included in a Demolition Takeoff?
A complete demolition takeoff includes the following elements:
- Structured to be removed: Walls, ceilings, flooring, roofing, foundations.
- Fixtures and finishes: Doors, windows, cabinetry, tiles, lighting.
- MEP Systems: Electrical wiring, plumbing, and HVAC systems marked for removal.
- Hazardous materials: Asbestos, lead-based paint, mold, or other contaminants flagged for abatement.
- Quantities and units: Square footage (drywall), linear feet (pipes), item counts (doors, fixtures).
- Debris disposal estimates: Debris volume, weight, and special handling needs.
Types of Demolition: Selective vs. Complete Demolition
There are 2 main types of demolition takeoffs, each affecting your estimation process differently.
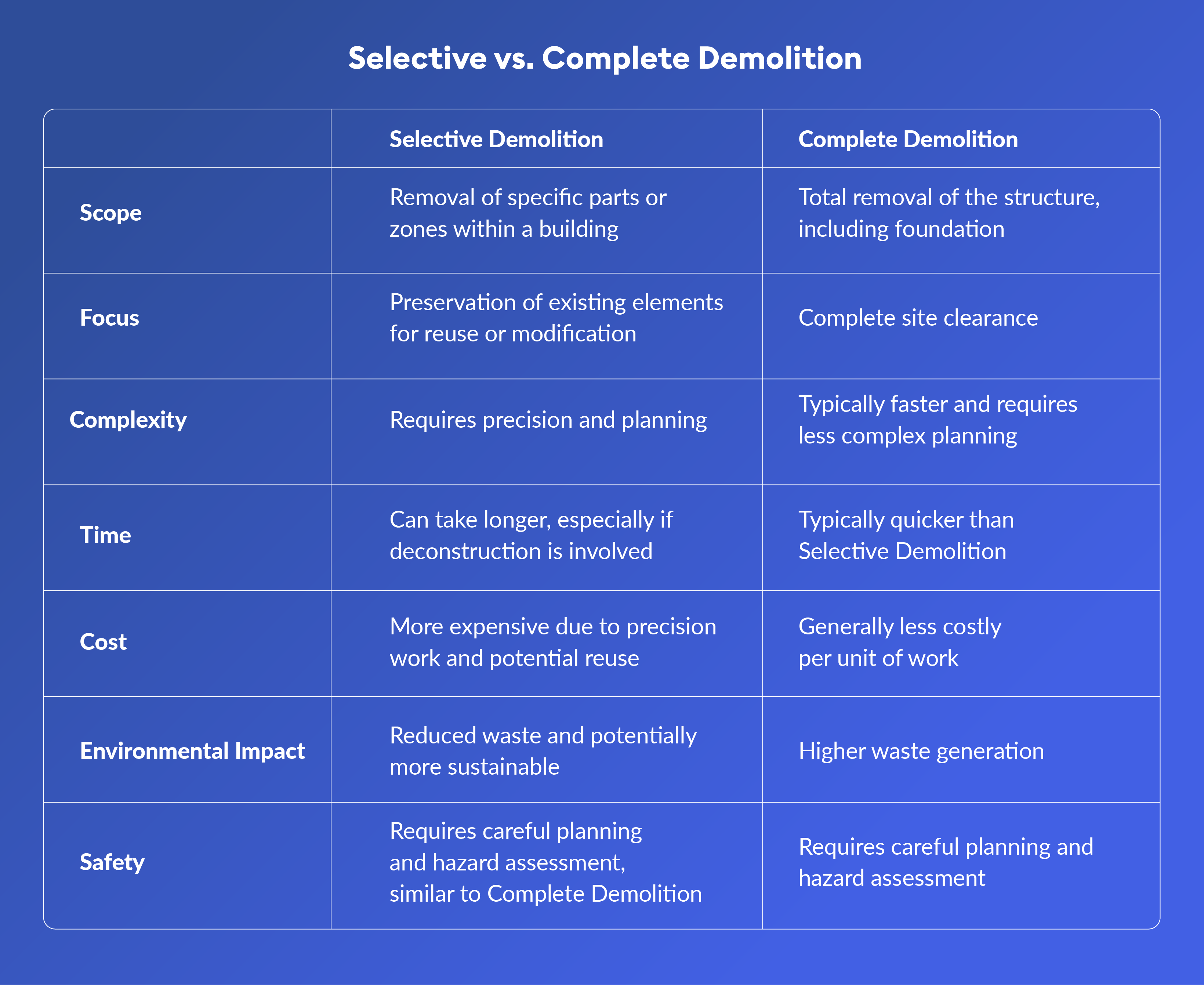
Selective demolition (also known as interior demolition) and Complete demolition require completely different takeoff strategies. The former focuses on carefully removing certain sections of a structure. This obviously requires more detailed planning around materials, recycling, reusing, removal of leftover debris, and hazardous materials. The latter, complete demolition, is slightly more straightforward. It requires the total removal of a structure, foundations included, and typically involves a less complex plan of action.
What Are The 3 Methods of Demolition?
There are three primary methods of demolition, each affecting how you plan your demolition takeoffs:
- Mechanical Demolition: This method uses machinery like wrecking balls, excavators, and other heavy equipment to break down a structure. It is commonly used for complete demolition, where the entire structure is removed.
- Explosive Demolition (Implosion): This method uses explosives strategically placed within a structure to cause a controlled collapse. It is often used for taller buildings and requires careful planning and safety measures.
- Deconstruction/Dismantling: Selective demolition and Deconstruction are essentially the same process, emphasizing controlled and careful removal of certain parts of a structure for reuse or recycling rather than complete destruction.
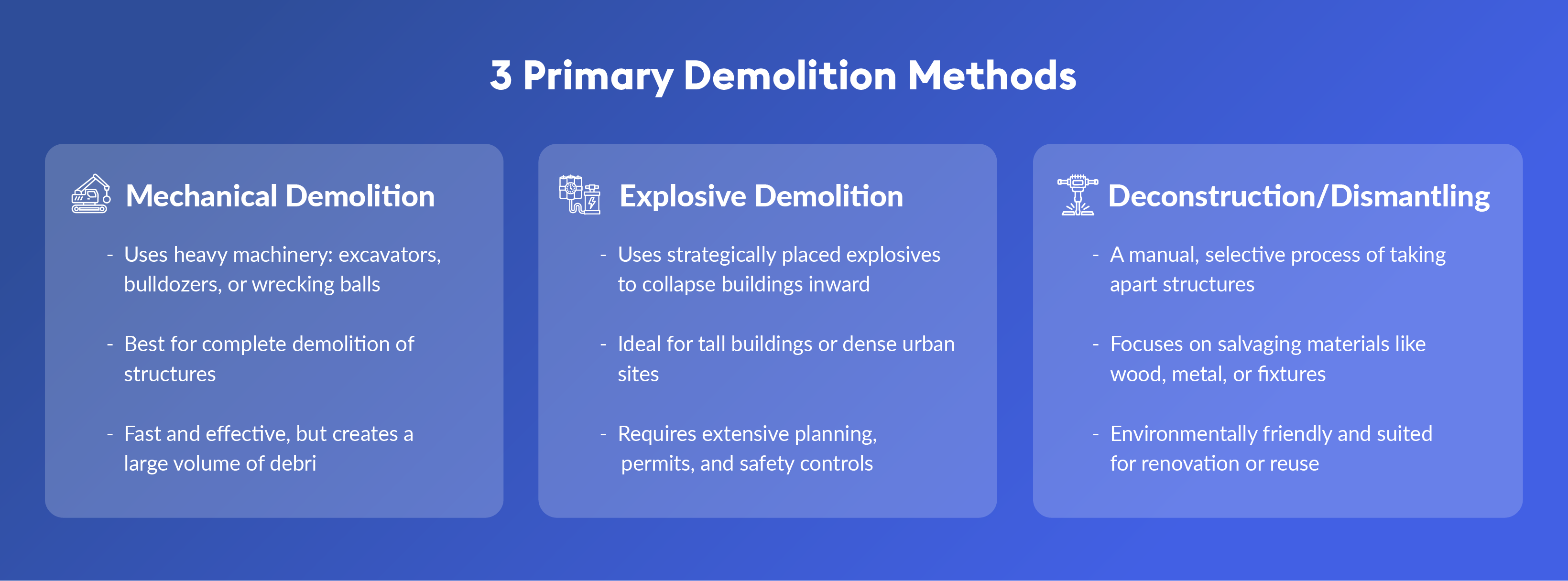
Now that we’re well acquainted with the fundamentals, let's dive into creating a demolition takeoff.
How to Create a Demolition Takeoff ( A 7-Step Guide)
An accurate demolition takeoff isn’t just about removing things —it’s about planning with precision, accounting for all variables, and ensuring your estimate reflects the real conditions on site.
Whether bidding for a project or building a detailed preconstruction plan, following a structured takeoff process is critical to staying on time and avoiding costly overheads.
Here’s a step-by-step guide to getting it right:
Step 1: Review the Project Scope and drawings
Let’s say you’re bidding on a hotel lobby demolition project. The scope calls for “demo existing reception area,” but during your review, you notice the hotel’s electrical panel is behind the reception wall. If you missed that, you'd risk demoing a critical system and delaying the entire project.
Hence, before you begin a demolition takeoff, review all project documentation—floor plans, demo drawings, MEP layouts, and any architectural notes.
Ask yourself:
- What exactly needs to be removed?
- Should I walk the site to confirm drawing accuracy?
- Does the plan match what’s visible on site?
- Have I identified all critical systems near demo zones?
- Are there elements marked “to remain” that could be mistakenly demoed?
Step 2: Identify and Quantify All Demolition Elements
Use the plans to determine everything that needs to be measured, then count and measure it. Then, break it down by material type and removal method.
Typical items:
- Flooring (tile, carpet, wood)
- Walls (gypsum, concrete, partitions)
- Ceilings (tiles, panels, fixtures)
- MEP systems (conduits, piping, ductwork)
- Doors, windows, millwork
- Hazardous materials (if flagged)
Before you start extracting quantities, take a moment to:
- Use drawings and site data to measure all items marked for removal.
- Break down elements by location, type (wall, flooring, ceiling), and removal method.
- Identify whether the demo is selective or full-structure.
- Don’t overlook materials that need abatement or special handling.
Manually identifying and counting quantities can be tedious and error-prone, especially under tight deadlines and competitive bidding conditions. Beam AI automates your demolition takeoffs, saving 90% of your time and enabling you to submit up to 30% more bids, confidently.
Not convinced? Learn how JZ Demolition doubled its revenue and saved 6 hours/day using Beam AI.
Step 3: Estimate Labor Requirements
You’re removing tile flooring from a small hospital corridor. It’s glued to the floor, access is tight, and patient areas are active. This means: no heavy equipment, hand tools only, and dust and debris must be controlled. You assign a 3-person crew over 3 days, factoring in slow progress, dust barriers, and cleanup time.
Estimating labor requirements is a crucial step in the demolition process. You must:
- Consider the demolition method (manual, mechanical, or hybrid).
- Evaluate access constraints, noise/dust restrictions, and protection needs.
- Assign crew sizes and durations based on production rates and site complexity.
- Include prep time, clean-up, and coordination with other trades.
Step 4: List Equipment and Tool Requirements
Figure out which tools and equipment you’ll need for each task and how long you’ll need them. Site access should also be considered for delivery and operation.
- List all required tools and machines per task (e.g., jackhammers, skid steers, lifts).
- Check site access for delivery and use of large equipment.
- Include PPE and hazmat gear as needed.
- Factor in equipment mobilization and daily rental costs.
Common tools and equipment:
- Mini-excavators, skid steers
- Jackhammers, grinders, saws
- Dumpsters, lifts, scaffolds
- PPE and specialty hazmat gear
Step 5: Calculate Debris Volume and Disposal Costs
Estimate the amount of debris generated and the cost of hauling it away. Consider local dump fees, recycling rules, and hauling logistics.
- Estimate debris volume using takeoff data (SF × depth ÷ 27 for CY).
- Classify debris by type: general (drywall), recyclable (metal), or hazardous.
- Calculate costs based on dump fees, transport distance, and hauler minimums.
- Include labor time for loading and staging.
Debris types include:
- General debris (drywall, wood, flooring)
- Concrete and masonry
- Metals (salvageable vs. scrap)
- Hazardous waste
Step 6: Account for Hazardous Materials
Older buildings often contain asbestos, lead paint, or mold. These require professional abatement and must be priced separately in your takeoff.
- Flag suspicious finishes (e.g., popcorn ceilings, vinyl tile, pipe wrap).
- Confirm with lab testing before pricing abatement.
- Estimate licensed removal, containment, and disposal separately.
- Align with local regulations (EPA, OSHA) for handling and reporting.
Check for:
- Suspicious finishes (e.g., popcorn ceiling)
- Old insulation or duct tape
- Vinyl tiles or pipe wrap
- Red flags in building age
Step 7: Include Contingencies and Final Review
Even the most meticulously planned demolition takeoffs can encounter surprises— hidden utilities, undocumented structural elements, or materials that don’t match the drawings. That’s why including contingencies in your demolition takeoff is a must.
- Add a 10–15% contingency to cover unknowns (hidden utilities, undocumented materials).
- Cross-check quantities, tools, and crew allocations with a second estimator.
- Review the plan with the project manager, safety officer, and superintendent.
- Align on demo sequencing, safety protocols, and on-site logistics.
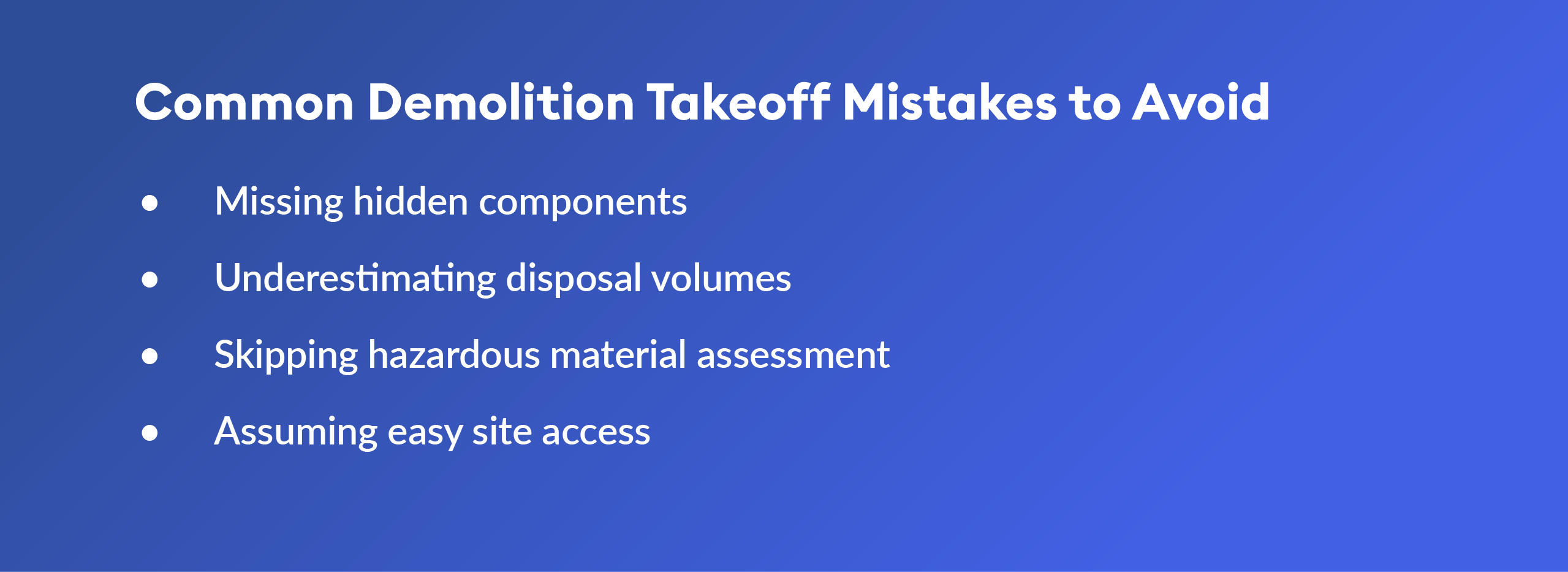
Every successful project begins with a detailed, accurate demolition takeoff. Follow the step-by-step guide, avoid common pitfalls, and let smart tools like Beam AI automate the heavy lifting for you!
Smarter, Faster, Sharper: Tech for Demolition Takeoffs
Gone are the days of traditional takeoffs and endless manual quantity counting. Beam AI automates the entire process for you, making demolition takeoffs faster and more accurate.
With Beam AI:
- Save 90% of the time spent on takeoffs
- Push up to 30% more bids
- Auto-detect specs and keyed-in notes
200+ construction businesses trust Beam AI. Learn how they are transforming their takeoffs. Book a demo now!
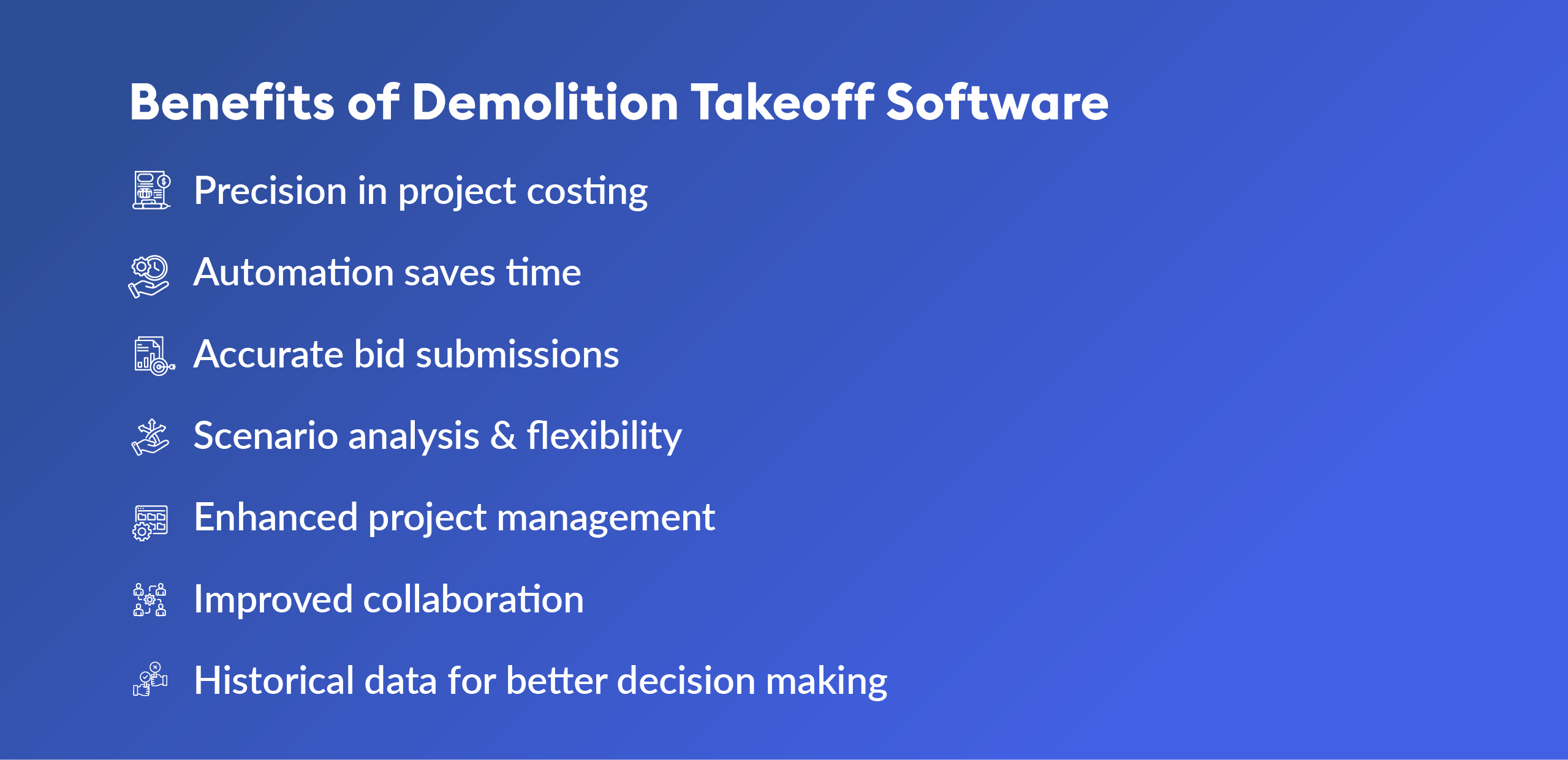
Before You Go
Demolition takeoffs might not be the flashiest part of construction, but they’re among the most crucial. A single oversight can derail your schedule, inflate costs, or compromise safety.
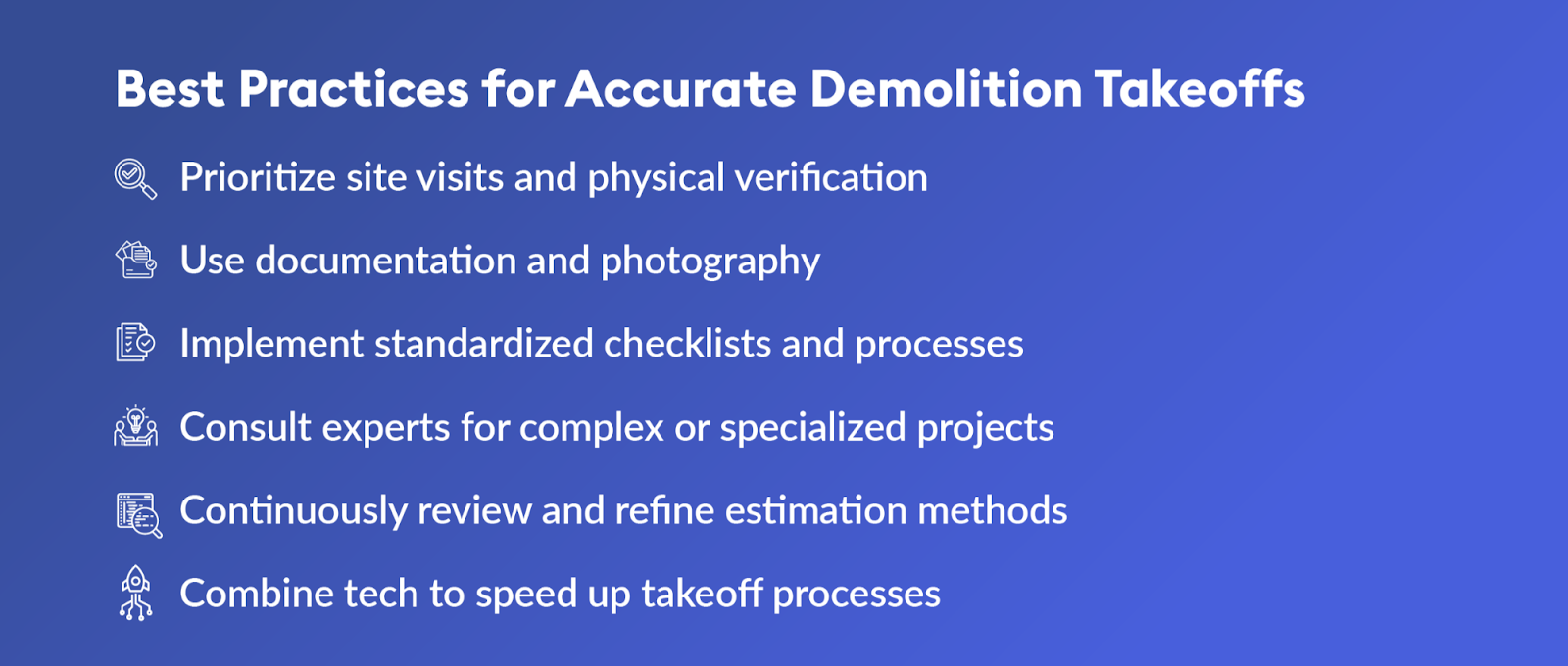
By mastering the fundamentals, following a structured takeoff process, and leveraging smart automation tools, you can bring precision, speed, and confidence to every estimate. Whether you’re tackling a selective teardown or a complete structural removal, accurate demolition takeoffs lay the groundwork for a successful build. Get them right, and everything else gets easier.